school
Formula Sae 2024-2025 Season
For my final year of being on UBC FSAE, I take a step back from design-oriented projects and focus on more research based projects for the season.These projects are all work-in-progress, so I will update this page as the project develops. Check back for updates!
Cornering simulation development
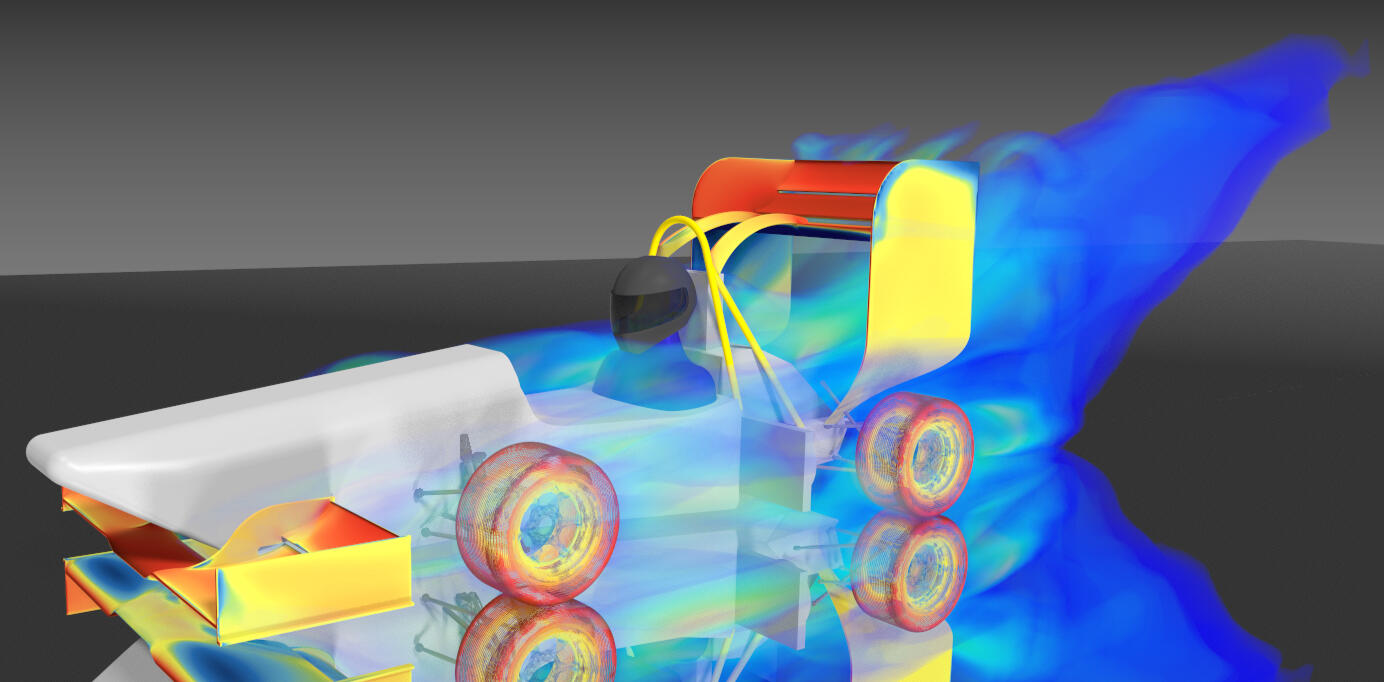
Context
Our team currently doesn't have the capability to simulate the vehicle's aerodynamic behavior during cornering in Star CCM+. Design judges in past competitions have asked us to demonstrate this, but we didn’t have an answer. This is a fundamental issue since the car is cornering more often than not!Not only could we lose points in the design category during competitions, but it also means our design choices lack justification when it comes to cornering performance.
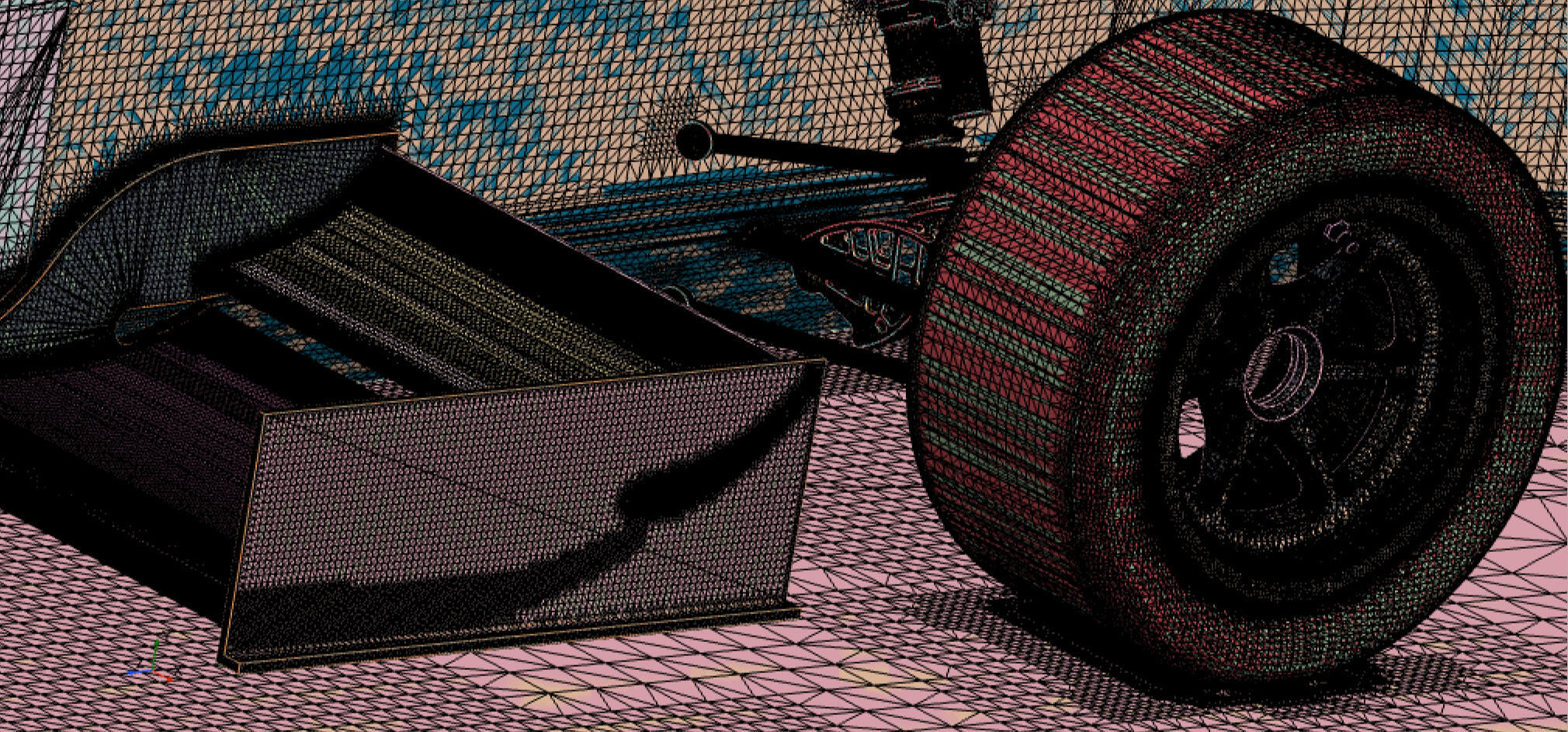
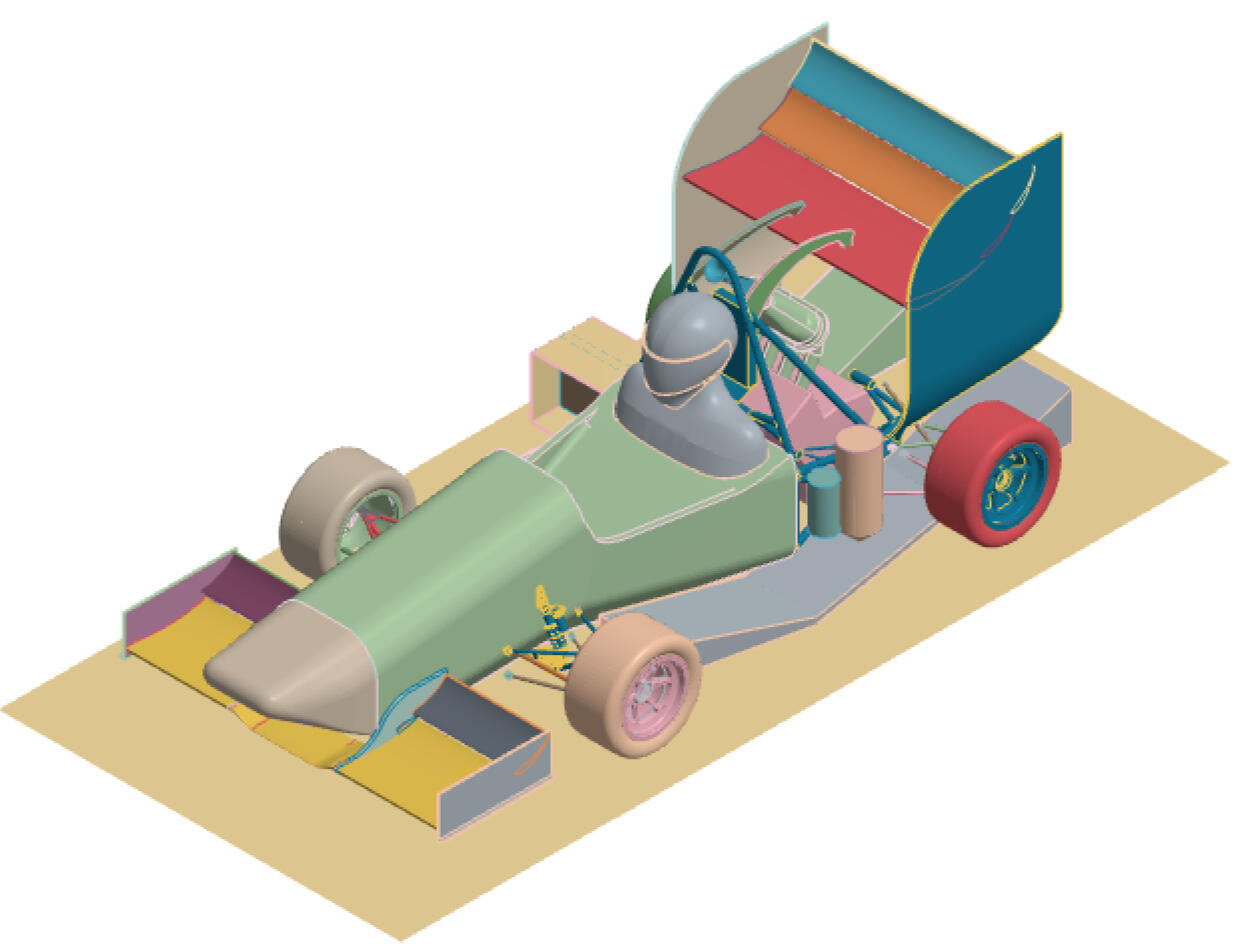
Approach
To tackle this, I’ll be developing our full car simulation template in Star CCM+ to support cornering simulations. The main challenge here is researching, developing, and testing a new template that includes cornering capabilities.This will involve automating steering angles, setting up complex domain boundary conditions, adjusting meshing controls, and plenty of trial and error!
project goal
My goal is to allow users to simulate the full car with any aerodynamic package configuration and generate a map of varying Cd and Cl values at different yaw angles during cornering.Once we have this cornering data, I’ll integrate it into our internally developed MATLAB lap time simulation for a more accurate lap time prediction. This will enable us to thoroughly evaluate and justify our design choices by comparing performance across various designs with different cornering maps.
Surface oil flow visibility development
The second project I am working on this year is the development of Surface Oil Flow Visibility procedures for our team.
Context
Validation is essential to complement CFD, but since we lack access to large wind tunnels for full scale testing, we have to get creative!One approach is to use Surface Oil Flow Visibility (SOFV), a custom mix of bright pigment and oil. There isn’t an off-the-shelf product available, so teams often develop their own. The previous year tried, but failed. In the image below, you can see one of our mixtures, which dried too quickly.Getting the right mixture involves a lot of testing and trial and error!
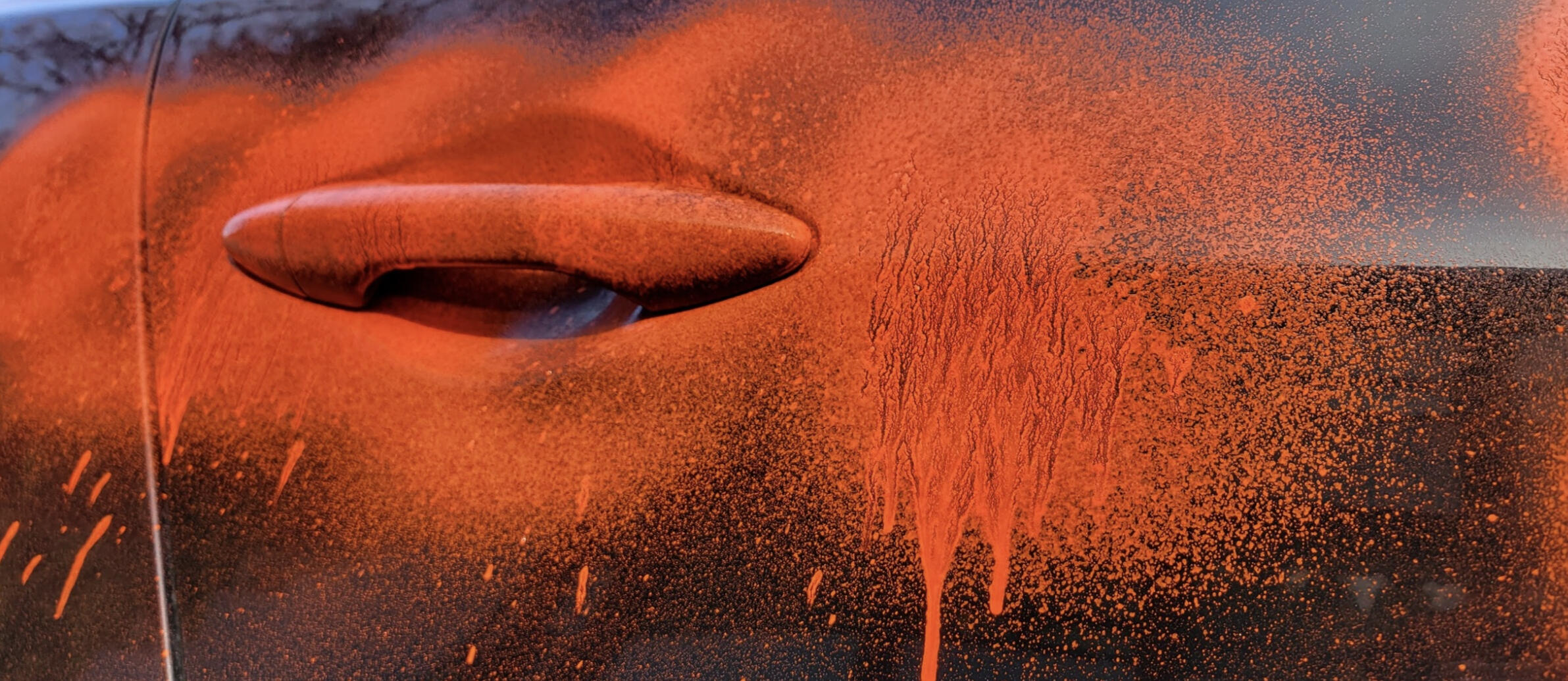

approach
To develop this, I plan to use UBC's Parkinson Wind Tunnel to replicate our running speeds during test days. I'll create an arbitrary aerodynamic shape with a carbon fiber surface finish that mimics our competition vehicle. This will be tested in the wind tunnel with various SOFV mixtures to determine the most suitable one.As a complementary validation exercise, I'll simulate the same wind tunnel in CFD and compare the flow patterns revealed by the SOFV mixture with those from Star CCM+.We have acquired kerosene and titanium dioxide which will be used to conduct our SOFV tests.
Star CCM+
Below are some miscallaneous images that show me going through the process of developing the mesh. I go through steps of prism layer refinement, wake refinement, and domain surface controls.The final mesh wasn't 100% satisfactory, but was good enough to use as a starting point. I set up y+ surface monitors so that once the simulation was complete, I can go back and check whether or not the target y+ of 1 is met on all surfaces, and use that to reiterate.Note: I later ran the simulation and had some results which were not satisfactory, I am working on improving these simulations and will provide some nice photos when ready!
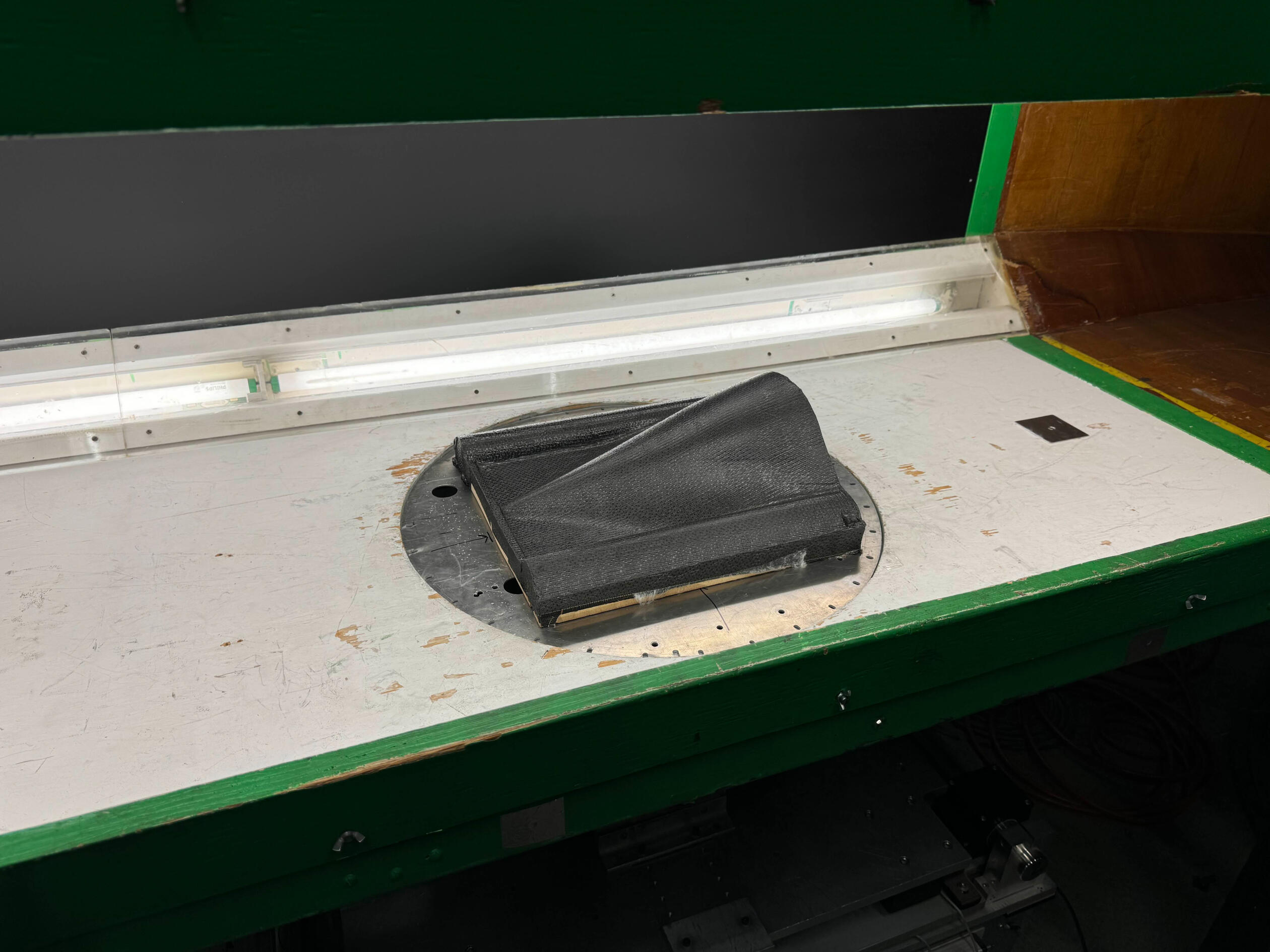
results
After many iterations with various mixtures, here are some notable results below. Both results here use paint thinner as a medium, but the left uses a red pigment powder, while the right uses a yellow oil paint.The paint works much better, and has the ideal properties in terms of dye suspension, viscosity, and drying time and behavior. Looking at both of these mixtures, we can identify flow separation regions where the fluid gets pushed backwards. A problem that we discovered during this was that the carbon surface was too porous, and we lost resolution of the flow lines within the paint. To counteract this, we are planning further trials using a clearcoated surface, as well as testing during track days.
Another interesting result was the mixture of titanium dioxide and water. While the water wicks up into a ball, and doesn't dry effectively, it is sure pretty to watch! Perhaps we could use this with a Go-Pro mounted to watch surface flows on track days?
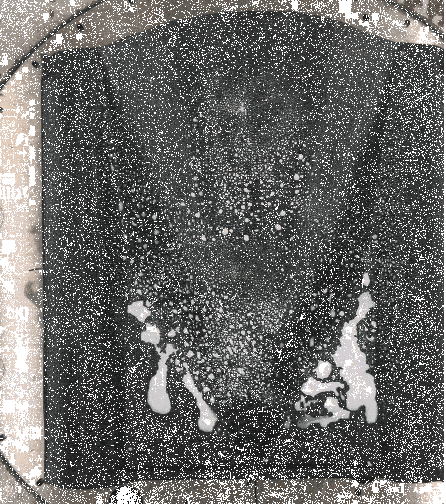
Next steps
While we have some interesting candidates, this mixture needs to be refined. I need to continue testing in both wind tunnel and during track days, using different mixtures at different concentrations. Additionally, I need to introduce additives to fine tune properties such as viscosity and drying time. Once this is all done, I will create a SOP or recipe sheet, so in the future our team can reproduce the mixture at any time, and use this for validation purposes.
project goal
Once developed, we can use SOFV during test days to observe real-world airflow behavior and, hopefully, enhance the accuracy of our CFD simulations.